Real-Time Assembly Instructions and Visual Aids
Real-Time Assembly Guidance
Real-time assembly instructions, powered by augmented reality (AR), offer a significant leap forward in automotive manufacturing. Instead of relying on static manuals, workers receive overlaid, step-by-step guidance directly on the assembly line. This dynamic feedback system allows for immediate corrections and prevents costly errors, ensuring components are placed correctly the first time. The AR interface can be personalized for each worker, adapting to their skill level and individual needs, further enhancing efficiency and accuracy.
Imagine a technician assembling a complex engine component. Using AR, they see precise 3D models of the part overlaid onto the actual physical component. Instructions appear as holographic prompts, guiding the technician through each step, highlighting critical assembly points and potential pitfalls. This eliminates the need for lengthy training periods and reduces the risk of human error, significantly increasing overall productivity.
Visual Aids for Complex Procedures
Visual aids, crucial for intricate assembly procedures, are revolutionized by AR. AR overlays provide detailed, interactive visualizations of complex assembly sequences, allowing workers to understand the intricate relationships between different parts before they even begin. This preemptive understanding reduces the likelihood of mistakes and ensures consistency in assembly procedures.
For instance, when assembling a multi-part chassis, AR can display a 3D model of the entire structure. Workers can zoom in and rotate the model to visualize the precise alignment of various components, and see how each piece connects to the others. This eliminates the need for a separate, potentially large, 2D diagram and allows for a far more intuitive and immersive learning experience, improving the quality of work and reducing the time for each assembly task.
Enhanced Training and Onboarding
AR significantly improves training and onboarding procedures in automotive manufacturing. Interactive 3D models and step-by-step instructions, displayed directly on the work area, provide an engaging and personalized learning experience. New hires can learn at their own pace, receiving real-time feedback and support from experienced technicians, reducing the time needed to bring them up to speed.
This dynamic approach to training allows for a comprehensive understanding of complex procedures, promoting faster learning and higher retention rates. By leveraging AR, manufacturers can also track trainee progress and tailor training programs based on individual needs, optimizing the development of skilled workers and promoting a more efficient and effective workplace.
Improved Safety Procedures
AR applications in automotive assembly can also enhance safety procedures by providing real-time warnings and alerts. The system can overlay safety guidelines and potential hazards onto the assembly line, ensuring workers are aware of critical safety protocols. This proactive approach can prevent accidents and minimize the risk of injuries, leading to a safer working environment for all employees. The system can even be programmed to identify potential safety risks, providing alerts to management and workers in advance, reducing the likelihood of accidents before they occur.
Maintenance and Troubleshooting Capabilities
Beyond assembly, AR can revolutionize maintenance and troubleshooting procedures. Workers can access detailed diagrams and instructions for specific equipment, overlaying them onto the machine for instant visual guidance. This real-time support can identify potential issues early on, enabling proactive maintenance and reducing downtime. AR applications can also provide detailed step-by-step instructions for troubleshooting, empowering technicians to quickly resolve problems and minimize disruptions in production.
For example, an AR overlay showing the inner workings of a complex engine component allows a technician to pinpoint the source of a malfunction without needing extensive disassembly. By guiding them through the repair process with interactive diagrams and step-by-step instructions, AR can significantly improve the efficiency and effectiveness of maintenance and troubleshooting, ultimately reducing repair time and maximizing productivity.
Improving Efficiency and Reducing Errors
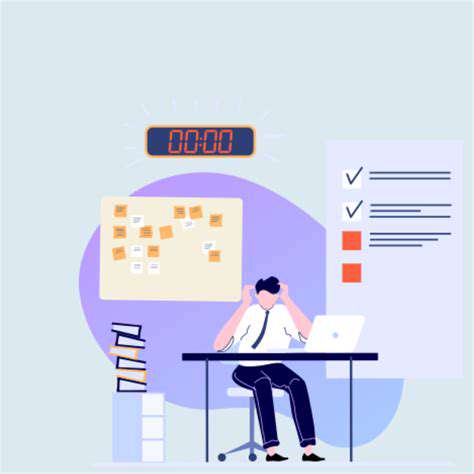
Streamlining Workflows
Efficient workflows are crucial for any organization looking to maximize productivity and minimize wasted time. Streamlining workflows involves analyzing existing processes, identifying bottlenecks, and implementing improvements to optimize the flow of work. This often includes re-evaluating task assignments, consolidating redundant steps, and leveraging technology to automate repetitive tasks. By focusing on these areas, companies can create a more streamlined and productive environment.
Optimizing Resource Allocation
Effective resource allocation is essential for maximizing output and minimizing waste. This involves carefully considering the skills and expertise of your team members and assigning tasks accordingly. Understanding the strengths and weaknesses of each team member can significantly improve project outcomes. Proper resource allocation also includes ensuring that the necessary tools, materials, and technology are available to support the work that needs to be done.
Implementing Technology Solutions
Technology plays a vital role in enhancing efficiency and productivity. Implementing the right software and tools can automate repetitive tasks, improve communication, and enhance collaboration. This can range from project management software to communication platforms. Choosing the right technology solutions requires careful consideration of the specific needs of the organization. This is crucial for maximizing the return on investment.
Enhancing Communication and Collaboration
Clear communication and effective collaboration are paramount in any organization. Promoting open communication channels and encouraging teamwork can significantly improve efficiency. Effective communication ensures that everyone is on the same page and working towards shared goals. This can be achieved through regular meetings, clear documentation, and utilizing communication tools. Encouraging collaboration creates a more supportive and productive work environment.
Measuring and Monitoring Progress
Regularly monitoring progress is essential to ensure that efficiency improvements are having the desired effect. Setting clear KPIs (Key Performance Indicators) can help track progress and identify areas for further optimization. This data-driven approach allows for adjustments to be made in real-time, ensuring that strategies remain aligned with goals. Monitoring progress also helps to identify any potential issues early on, allowing for proactive solutions to be implemented.
Training and Development Initiatives
Investing in employee training and development is crucial for improving skills and enhancing efficiency. Upskilling employees can increase their productivity and allow them to take on more complex tasks. A well-trained workforce is more adaptable to changes and better equipped to handle new challenges. This investment in human capital often yields significant returns in the long run.
Promoting a Culture of Efficiency
A supportive and collaborative work environment can greatly enhance efficiency. Promoting a culture of continuous improvement and encouraging employees to share ideas can foster innovation. By emphasizing efficiency and productivity, companies can create a positive work environment where employees feel valued and motivated. Implementing clear goals and expectations, along with regular feedback, is vital for cultivating this culture.
Optimizing Maintenance and Troubleshooting
Improving Efficiency Through Proactive Maintenance
Proactive maintenance strategies are crucial for optimizing maintenance and troubleshooting in automotive manufacturing. By implementing scheduled inspections, preventative maintenance tasks, and predictive maintenance techniques, manufacturers can significantly reduce unplanned downtime and minimize costly repairs. This proactive approach allows for the identification and resolution of potential issues before they escalate, ensuring consistent production output and minimizing the impact on the overall assembly process. A well-defined maintenance schedule, coupled with readily available parts and skilled technicians, forms the bedrock of a robust proactive maintenance strategy.
Implementing condition-based monitoring systems, which use sensors to detect subtle changes in machine performance, can further enhance proactive maintenance. This data-driven approach allows for the early identification of potential failures, enabling preventative actions before significant equipment damage occurs. This not only reduces downtime but also extends the lifespan of the machinery and reduces the need for costly repairs.
Troubleshooting Common Assembly Line Issues
Troubleshooting assembly line issues effectively is paramount to maintaining production flow and minimizing delays. A systematic approach is essential, involving detailed documentation of the issue, a thorough analysis of the problem's root cause, and the implementation of effective corrective actions. This includes careful observation of the assembly process, analysis of any faulty parts or components, and verification that the solution effectively addresses the problem.
Effective troubleshooting also requires a well-defined communication channel within the manufacturing team. Open communication between technicians, engineers, and supervisors facilitates a collaborative approach to problem-solving, ensuring that everyone is aware of the issue and working towards a solution. A clear understanding of the assembly procedures, combined with a well-maintained troubleshooting guide, assists in identifying and resolving issues swiftly and efficiently.
Optimizing Maintenance Schedules for Enhanced Production
Optimizing maintenance schedules is a key factor in maximizing production output and minimizing downtime in automotive manufacturing. By carefully analyzing production schedules and maintenance requirements, manufacturers can develop a schedule that minimizes disruptions to the assembly line while ensuring the necessary upkeep of equipment. This includes considering the frequency of maintenance tasks, the duration of downtime required for each task, and the potential impact on production quotas.
Regular review and adjustment of the maintenance schedule are crucial for adapting to changing production demands and equipment needs. Flexibility in the schedule allows for addressing any unexpected issues or adjustments to the production line. This dynamic approach ensures that the maintenance schedule remains aligned with the overall production goals and minimizes disruptions to the assembly process.
Implementing a robust system for tracking maintenance activities is also essential. This allows for a clear understanding of the maintenance history of each piece of equipment, helping to anticipate potential problems and schedule maintenance accordingly. This data-driven approach to maintenance scheduling ensures efficient resource allocation and reduces the risk of equipment failures, ultimately optimizing production.
By integrating these considerations into the maintenance schedule, automotive manufacturers can significantly reduce downtime, improve production efficiency, and enhance the overall quality of the assembled vehicles.